THOUGHT LEADERSHIP
What is the best way to model complex water structures?
Understanding the behaviour of water as it flows in natural and constructed environments is fundamental to designing and managing many civil assets, and integral to reducing risk and cost in water infrastructure projects.
Water is such an intrinsic part of our lives that we all have a good observational understanding of what water is and what it does in many everyday situations, like falling from a tap or spiralling down a plug hole. But our intuition can only take us so far. When engineers design important infrastructure such as dam spillways, or inlets to pump stations, or need to understand issues such as fish passage for a low weir, they need to turn water into numbers and quantify its behaviour. Being able to quantify complex water flow is one way engineers can better understand the world and make a difference.
Modelling options
When water flow is complex and a deeper understanding of its behaviour is required, the two main options to help improve this understanding are physical scale models and computational fluid dynamic (CFD) models. But when should one be used over the other?
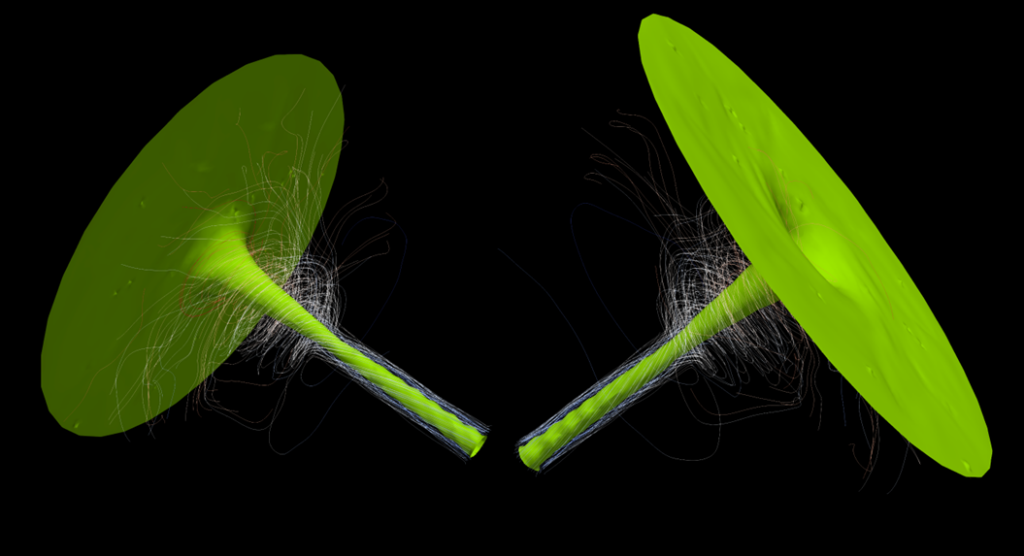
Physical scale models are created and used in a research laboratory, whereas CFD models are created using software and run on fast computers. Here ‘scale’ means the physical models are built at some fraction of the item of interest’s size. Historically, physical scale models have been the gold standard for helping understand complex water flow, but that’s not always the case now. Both methods have a place, and they can complement each other.
It’s generally better to use more advanced modelling techniques early in a project to better guide the design process or understand an existing system.
Has CFD killed the physical scale model star?
Knowledge about the physics of water flow has developed from centuries of physical observation with experiments run in hydraulics laboratories and the field, combined with theoretical calculations. Advances in computing performance in the last few decades have allowed these theoretical calculations to be solved in finer detail and with greater accuracy. But does this mean the end of physical scale modelling testing, in particular as computing power is growing faster than the number of research laboratories? Not for a while.
Even with advanced, powerful computing systems, the outputs of CFD software tools still need to be validated against physical measurements. For the physical scale of the civil engineering problems being solved (e.g. a dam spillway), the CFD models approximate the theoretical calculations, and these approximations need to be validated. Some water flow problems are dominated by well-defined forces, such as gravity, and these problems are easier to validate. But other problems are dominated by turbulence and multiphase flow, and these are harder to validate as the phenomena are more complex.
A note on turbulence and multiphase flow
In the aerospace and car industries, where the fluid of interest is air rather than water, a designer uses a combination of wind tunnel testing and CFD modelling to better understand the performance of a design. Small parts can be simulated in CFD with minimal approximations using direct numerical simulation (DNS) of turbulence. But for a full car and even more so for a large commercial aeroplane, it’s currently cost-prohibitive to only use DNS (e.g. millions of dollars per run), and some level of wind tunnel testing is still required. This is combined with non-DNS modelling CFD methods.
It’s similar in civil engineering. There are different physical sizes, stages of a project timeline, costs, and risks of getting the answer wrong. These drive the balance between CFD and physical scale model testing. Most work, in particular at a concept level, is done with CFD, but physical scale modelling is still recommended for critical infrastructure prior to construction.
A matter of scale
The size of most civil engineering infrastructure – such as spillways, rivers and large stormwater culverts – make it impractical to use DNS of turbulence (based on cost and timing).
Both physical scale models and CFD can be time-consuming tools to use, and for various projects it’s better to use one before the other. For the design of fish passages and recreational water systems (such as whitewater kayaking), doing small-scale, rough physical scale modelling can be efficient for design development of concepts. This is because designers can move 3D-printed shapes around in a hydraulic flume, and see and feel the direct impact on changes to the design. This is a very complex problem with few industry guidelines and without the same body of research as other civil engineering problems, such as dam spillways and energy dissipation.
Where there is a large body of knowledge on a topic, standard designs provide a starting point. Then, it’s often efficient to start with hand calculations or a concept-level CFD model. These calculations may lead to more detailed design, modifications of standard designs with detailed CFD modelling, and then, potentially, physical scale model testing. There are always iterations, and sometimes the CFD modelling can be used to inform the design of a physical scale model testing setup, and vice versa. CFD modelling is also faster and can more easily be used for design optimisation compared to physical modelling.
In some cases, using CFD alone is possible, particularly where there is a solid body of knowledge about a piece of infrastructure. The temptation is to use CFD more and more, as it can often be lower in cost. It is also important to note that physical scale model testing has its limitations. So there are cases where CFD modelling can provide more insight at a lower cost.
With physical scale model testing, the key limitation is in its name. The model is built at a much smaller scale than the feature being modelled – just a fraction of the expected final design or existing system size. Typically a coarse model of a dam or spillway may have a 1 in 200 scale, and a good one may be at a 1 in 50 scale. A 1 in 50 scale model of a spillway that was going to be 100 m high when finally constructed would need to be 2 m high as a model. This is okay for pure water models, but for aerated flow the ideal scale is closer to 1 in 10. So if aerated flow was important in that 100 m high spillway, then the model would be 10 m high. At that size it would not fit in a normal hydraulics laboratory and would be very expensive to build. So, typically, a compromise is made and a 1 in 30 model is constructed. The reason scale is important is that water behaves differently at different scales. For example, surface tension is important in a pipe that’s 5 mm in diameter but is not important in a large river flow.
How do you measure water?
Another limitation of physical scale model testing is measuring the flow during the experiment. There are some limitations on CFD as well but, compared to a physical scale model test, it is generally much easier to get the results from a CFD model accurately, in many more locations, and without disturbing the flow.
Complex models demand high-performance computing
Complex multiphase flows for fish passage and smaller whitewater kayak systems can be modelled well with scale models initially, as the system being modelled is relatively small. But when you’re modelling something that is much larger and has complex multiphase flows, scale model testing is harder. Model size is important for CFD models as well, and there is no free kick here. Larger systems where there is complex flow are computationally more expensive to model in detail using CFD. Typically, however, the budget of projects involving larger complex systems are also larger – and so, the modelling costs can be a similar proportion of the total project costs for small and large projects.
At some point in the future, such as when quantum computing becomes mainstream, CFD using direct turbulent simulation (i.e. DNS) of larger objects could completely replace physical scale modelling.
Room for both in pushing the knowledge envelope
Both physical scale modelling and CFD modelling require specialised facilities and experienced modellers. With the advent of lower cost computing services and increased CFD training in many engineering courses, CFD modelling has become the lower cost option for many civil engineering water modelling problems. But both physical scale modelling and CFD will continue to remain important for many years yet, and both approaches should be encouraged.
In general, what’s easy or difficult in physical scale modelling is often of a relatively similar level of difficulty for CFD modelling. Often the approach will come down to a modeller’s preference and access to either option, but in some cases it’s prescribed by standards. CFD is often cheaper and faster to set up for most civil engineering scale problems and, once set up, can be run on multiple computers at once and address more questions at once. Viewing the results of the CFD model is more flexible, but some prefer the touch and look of a physical scale model.
For novel phenomena at the edge of our understanding, there is still no substitute for a physical scale model. Over time, this will leave physical scale modelling mainly as a research tool and to aid community consultation and education, with CFD used for operational modelling in industry. Most projects will still use a combination of the two.
Like all good engineering projects, solving complex water modelling problems requires having adequate time and budget to provide a suitable quality result. When approaching a complex water flow problem, inform yourself of the solution options. The best model for your stage of understanding is the one that reduces uncertainty and improves knowledge to aid better decision-making.
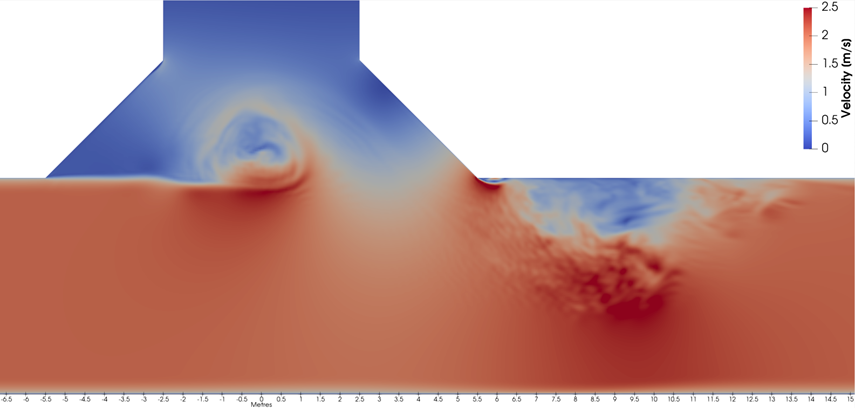
If you’d like to talk with Entura about your water or dam project, contact Phillip Ellerton (Australia) or Shekhar Prince (international).
About the author
Dr Colin Terry is a civil engineer at Entura with three decades of experience in Australia and New Zealand. His experience includes modelling, planning, design and construction support. He has worked on multidisciplinary projects across various parts of the water cycle including catchment management, water supply, hydropower, land development, transport, and water quality in natural systems – with a focus on surface and piped water.
MORE THOUGHT LEADERSHIP ARTICLES
September 28, 2023